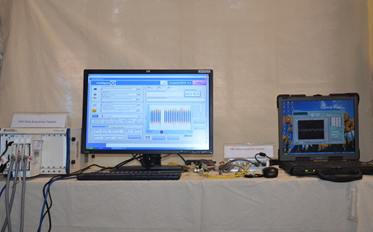
Estimation of Impact location and severity using strain response
Impact damages due to events such as tool drops, runway debris, hailstones etc. can reduce the load carrying capacity of composite structures. Often they result in barely visible impact damage (BVID) which are likely to be missed during visual inspection. Impact events are random in nature, in both time domain (when it will occur) and spatial domain (where it will occur). The challenge is to develop a smart impact monitoring system which will remain active to report any impact event on the structure.
Specifications:
FBG interrogator for in-flight data acquisition Wx-m (20 KHz, 4 channel with one sensor per channel)
NI PXIe based strain and Voltage data acquisition (100 kHz, 24 Channel Strain Data acquisitions)
Major milestones / results of this technique
Impact test setup is developed in-house for carrying out impact tests on composite structures. The portable impact tower comprises of a drop weight and a tup instrumented with a force sensor to measure the force response during impact. Sensor sensitivity studies are carried out to determine the optimum sensor locations on the structure. Fiber Bragg Grating (FBG) and Resistance Strain Gauges (RSG) sensors are used in this study to measure strains in the structure during impact. Algorithms based on Pearson’s linear correlation, LS-SVR and System identification techniques are developed to estimate impact location and severity. These algorithms are validated through several experiments. Real-time implementation is done using in-house developed software with GUI such as ImpactVIEW where strain data is monitored continuously. In case of an impact, the software trigger mechanism saves the strain response, estimates the location and energy/force, and presents the results to user in a GUI form.
Extensive experimentation was carried out based on building block approach. Several laminates of different thicknesses are tested first before moving on to more complex configurations such as stiffened skin panels and wing-box like structures. The probability of detection (POD) estimation shows that impact location can be estimated with in 100mm error in 90% of cases.
|
|
|
Location Estimation (Red Dot is the actual location ) |
POD Estimation for location estimation |
Online Implementation with ImpactVIEW |