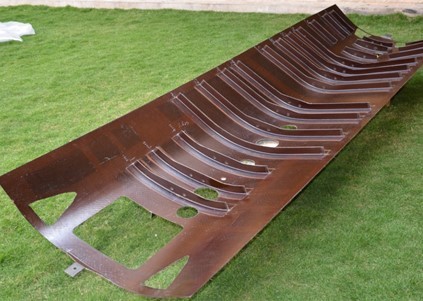
Design and Development of cocured composite structures for airframe using autoclave moulding
Autoclave processing of prepregs is a well-established process in the aircraft industry. It offers excellent reliability and part quality mandated for airworthy parts. A considerable progress has been made in the country in the area of composite structures with autoclave moulding and its application to national aircraft, rotorcraft and space programs. CSIR-NAL has developed cocuring technology indigenously to realise highly integral structures for aircraft programs. The primary benefits of cocuring are reduction in part count, elimination of fasteners, reduced assembly and associated costs and elimination of stress concentration zones due to fastener holes, elimination of fuel leakage etc.
The realisation of highly integrated structures for LCA-Tejas and SARAS aircrafts at CSIR-NAL shows the understanding and standardization of various tooling and manufacturing aspects of autoclave moulding technology. The total structure is realized in shorter time compared to the traditional fastened structure. Structures developed have undergone qualifications tests and cleared by relevant regulatory authorities. More than 25 LCA aircrafts have taken to skies with composite structures manufactured at CSIR-NAL and extensive flight testing has been done with composite parts performing excellently.
1. Conceptual level studies and layout preparation
2. Design of test matrix as per Building Block approach for design allowables and special features
3. Global and detailed FE analysis and stress reports for certification
4. CAD Models and Detail drawings for manufacturing
5. Design, development and qualification of external and internal tools
6. Manufacturing of cocured part and qualification by NDE using ultrasonic inspection and dimensional inspection
7. Extensive QA/QC documentation for materials, processes and equipment
This technology can be commercialized based on the specific structure that needs to be developed.
Co Cured Aircraft Parts through autoclave molding