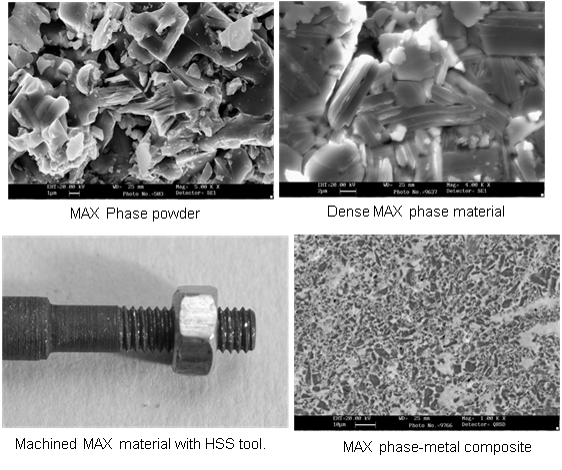
Structural Ceramics
1. Ceramic Matrix Composite through CVI
- Continuous fibre reinforced ceramic matrix composites (CFCMC) through hybrid processing technique such as Chemical Vapour Infiltration (CVI) process combined with polymer impregnation pyrolysis (PIP)/Liquid silicon infiltration (LSI) process
- CFCC with new interfaces and self-healing matrix/seal coating is being developed through CVI
- Ceramics and ceramic composites through nano infiltration Transient Eutectic (NITE) process
- Structure-property-processing correlation of the CFCC
- Development of Chemical vapour deposition (CVD)/CVI process for synthesising of high performance ceramics such as Pyrolytic graphite, Si3N4, B4C, Si-C-B-N etc.,
2. Ultra-High Temperature Ceramics
The transition metal borides (ZrB2, HfB2, TiB2), carbides (ZrC, HfC, TiC) and nitrides (ZrN, HfN, TiN) are grouped as ultra-high temperature ceramics (UHTCs), wherein their melting temperatures ≥3000°C, hardness ≥20 GPa and high modulus ≥400 GPa. UHTCs are considered to be capable of withstanding at temperature ≥2000°C for shorter durations and also good oxidation/erosion/wear resistance. The applications of UHTCs are nose-cone and thermal protection for re-entry vehicle, armor, cutting tools/wear resistant components, etc,. Generally, dense UHTCs have been produced at temperature ≥1800°C and longer durations. In CSIR-NAL, it is established that the dense monolithic and UHTC composites can be made at 1200-1500°C by reactive processing. The monolithic ZrC and TiC ceramics and TiN-TiB2, TiB2-TiC, ZrB2-ZrC, ZrB2-SiC and ZrB2-ZrC-SiC composites have been made at moderate temperature and pressure.
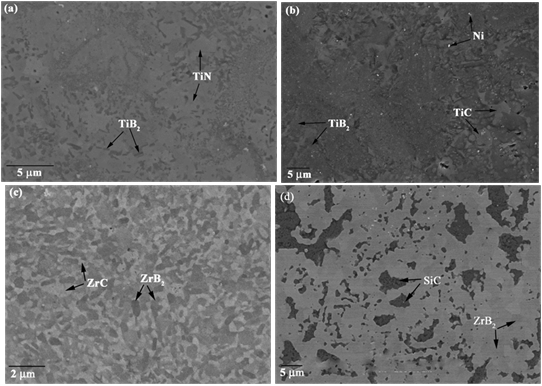
(a) TiN-TiB2 composite with 99% relative density. (b) TiB2-TiC composite with 99% relative density.(c) ZrB2-ZrC composite with 99% relative density. (d) ZrB2-SiC composite with 99% relative density.
3. MAX Phase composites
The MAX phase materials with the general formula Mn+1AXn (M: transition metal, A: Group IIIA element, X: carbon or nitrogen), where n=1 to 3. MAX phases are elastically stiff, are good thermal and electrical conductors, are resistant to chemical attack, and have relatively low thermal expansion coefficients. Mechanically, however, they cannot be more different; they are relatively soft and most readily machinable using conventional high-speed steel tools, excellent thermal shock resistant, and damage tolerant. Moreover, some are fatigue, creep, and oxidation resistant. Generally, the powders and dense MAX phase composites are produced by reactive processing. In CSIR-NAL, the high purity M3AX2 and M2AX phase powders have been produced at a reasonable temperature. The dense MAX phase composites have been made at moderate temperature and pressure.
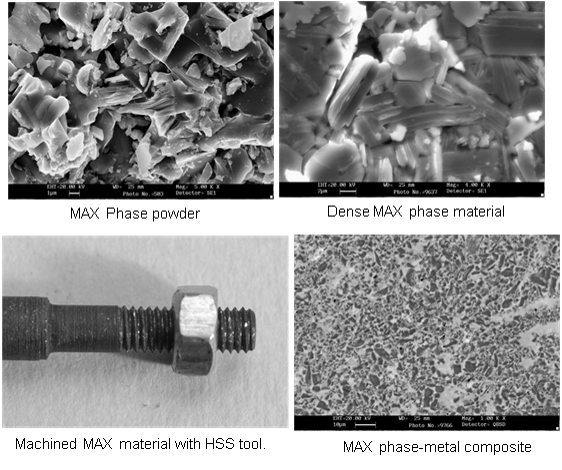
4. Polymer Derived Ceramic Matrix Composites (PDCMCs)
The precursors for polymer derived ceramics are soluble and deformable ceramic containing polymer at room temperature which will convert into various ceramics depends on the pyrolysis conditions. This type of ceramic polymer precursors can reduce the processing temperatures for making monolithic and ceramic composites. The continuous carbon fiber (Cf) reinforced ZrB2 or SiC based ceramic matrix composite are prepared through preceramic polymer impregnation and pyrolysis (PIP) process. ZrB2-based matrix is synthesized by considering ZrB2 as predominant phase rather than other materials and similarly, SiC based matrix materials. However, to synthesis ZrB2 based composite ZrB2 particles along with preceramic polymer precursors which will produce SiC/Si3N4/SiCN/SiOC is used during PIP process. PDCMCs are produced either completely by PIP process or hot pressing followed by PIP process. The method has been established to make PDCMC at moderate pressure and also by pressureless PIP process. Hence, this economic method is suitable to replace commercially available high-pressure processing method as well as long duration processing method to produce carbon fiber reinforce ceramic matrix composite. PDCMCs are suitable for wear resistance, corrosion resistance, high temperature / ultra-high temperature applications.
5. Processing and consolidation of advanced ceramics
The materials Science Division has been involved in research and development in the area of synthesis, processing and consolidation of advanced ceramic materials for potential applications in aerospace and other sectors of societal impact. Methodology has been optimised for preparing variety of fine ceramic powders for specific applications. Expertise has being developed on colloidal or wet processing of commercial or indigenous ceramic materials like alumina, silica, zircon, silicon carbide, silicon nitride, calcium phosphate etc., and their consolidation by slip casting and gel casting to fabricate some strategic components like after burner cups, ceramic radome, porous scaffolds etc. Continuous research effort in the area of shaping has lead to the development of a novel additive manufacturing method called “mouldless casting” of ceramics. Development of EBC materials and coating systems for CfSiC composites for high temperature engine applications is under progress.